Every modern supply chain is faced with increased demands and ever-increasing cost pressures. According to the ‘seven Rs of logistics’, the following must be provided:
the right product
in the right quantity
at the right time
in the right quality
in the right place
at the right cost
to the right customer
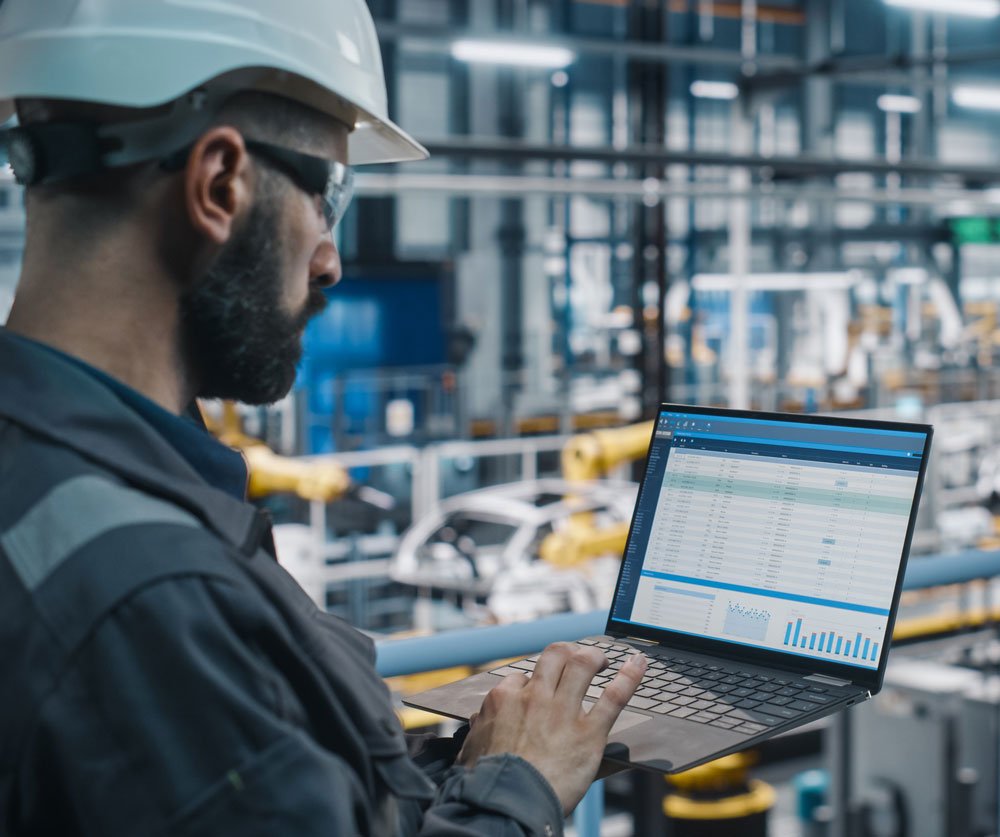
With the Supply Chain Management module, you can optimise all aspects of your warehouse management and optimally integrate higher-level modules such as production and/or merchandise management.
Your advantages:
Secure
Secure:
In connection with the apintra Production module, the supply of the producing areas with direct goods such as raw materials, auxiliary materials and operating supplies as well as vendor parts and semi-finished products is ensured. Equally secure is the supply of indirect goods such as office supplies, spare parts or services.
Save
Save:
With the Materials Management module, you uncover potential savings and can use them directly. For example, you can weigh up the costs for the provision of goods (readiness for delivery or service level) and the costs for a quantity that is required but not available (shortage costs/shortages) and thus optimise costs.
Reduce
Reduce:
Get an accurate overview of excessively high stock levels or slow-moving items and reduce the capital tied up in inventories (capital commitment costs) by reducing these inventories in a targeted manner.
General
- Dialogue capture with instant processing
- Master data management with classification
- Alternative units
- Incidental procurement costs
- Material-related replenishment time
- Material movement
- Parameterizable ABC analysis
- Multi-level inventory management
Statistics
- Supplier requests
- Open orders
- Reserved quantities
- Consumption
- Price statistics
- Average purchase price
- Replacement times
Ordering
- Automatic order proposal and requirements calculation
- Order requests and administration
- Supplier discounts
- Stock shortfalls
- Range calculation
- Material return delivery/debit note for supplier
- Processing of safety-relevant parts
- RFID management
- Foreign currency
- Supplier reminders
- Delivery and invoice receipt control
- Capital requirements assessment
- Determination of requirements with consideration of production lists
- Missing quantity determination and material postings
The apintra® advantages
All apintra® solutions are based on the same technology with equal advantages. These include multi-client capability, plausibility checks, open interfaces and local and temporal availability, as well as the ability to quickly find each individual data record.
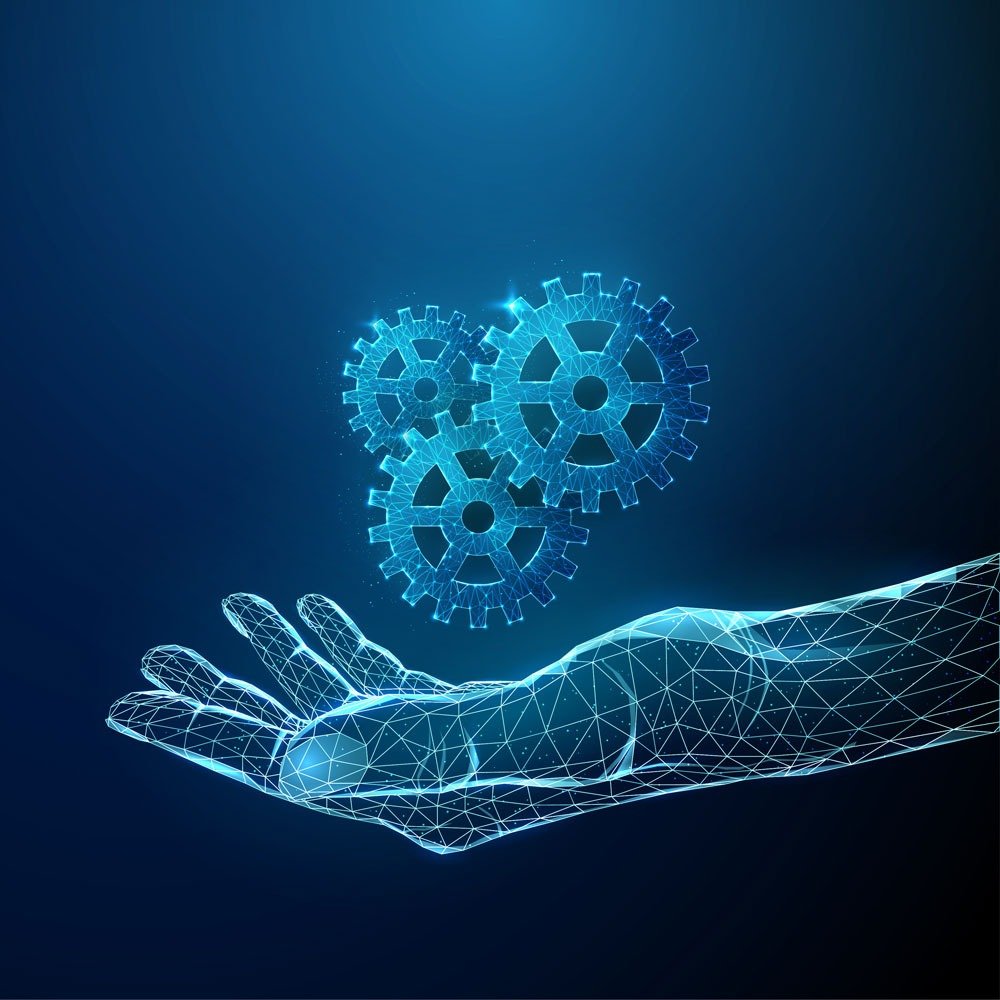