PRODUKTIONSPLANUNGS- UND STEUERUNGSSYSTEM (PPS)
Was sie bei uns erwarten können
Sie erwarten zurecht von einem optimalen Produktionsplanungs- und Steuerungssystem (PPS), dass es flexibel auf sich verändernde Produktionsprozesse reagiert.
Es bietet Variabilität und einfachste Korrekturmöglichkeiten. Alle Positionen sind nachträglich dynamisch bis zur Produktionseinlastung (Positionsebene) veränderbar.
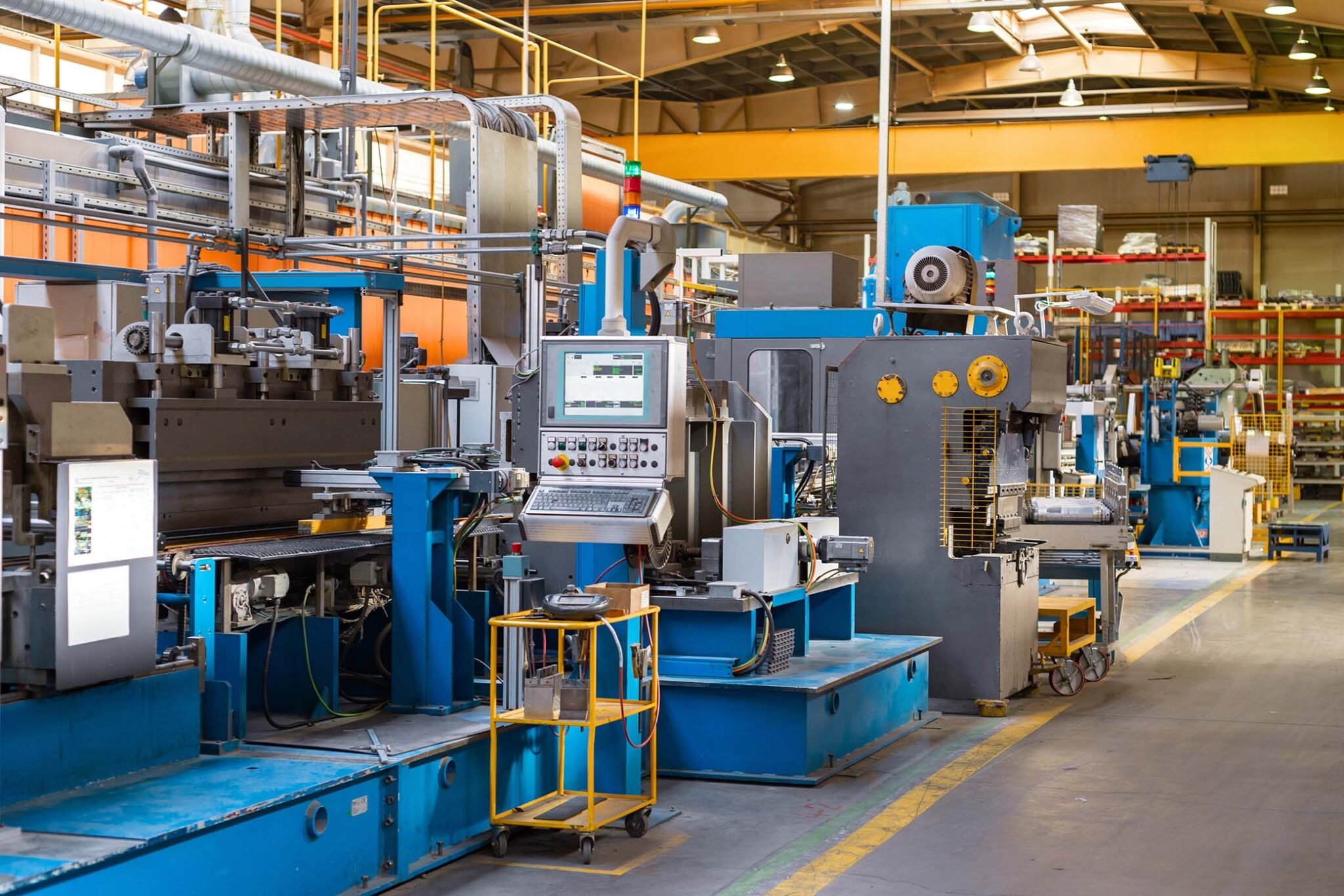
Andere Systeme sind sehr aufwendig
Bei Änderungen oder Varianten einzelner Produkte müssen die Daten für die Stücklisten bei vielen System aufwendig neu konfiguriert werden.
Bei apintra ist das anders:
Sie geben in das apintra® Produktionssystem die gewünschten Änderungen ein. Unsere Netzplantechnik kalkuliert den sich geänderten Materialbedarf, die Kapazitäten und erzeugt daraus die neue Fertigungsplanung.
Als Ergebnis erhalten Sie einen vollständig optimierten Produktionsplan, komplett mit Stücklisten bis in die X. Stufe, sowie dem gesamten Arbeitsplan für Personal und Maschinen (um einen kompletten Kleinwagen abbilden zu können, sind nicht mehr als 10 Stufen nötig).
Sie profitieren davon, wenn...
Sie variable Produkte herstellen
Sie komplexe Produkte produzieren
Sie bis zum eigentlichen Produktionsprozess Änderungen an der Stückliste oder den verwendeten Teilen vornehmen wollen
Sie variabel entscheiden wollen, ob sie Teilbereiche statt selbst zu produzieren extern fertigen lassen oder zukaufen
Sie einfach Flexibilität in der Fertigung benötigen,
und vieles mehr…
apintra® Lösung
Alle apintra® Lösungen basieren auf der selben Technologie mit den gleichen Vorteilen. Darunter sind Mandantenfähigkeit, Plausibilitätsprüfung, offene Schnittstellen, örtliche und zeitliche Verfügbarkeit, sowie das schnelle Finden jedes einzelnen Datensatzes.
Das apintra® Stücklistenwesen
In unserem Stücklistenwesen unterscheiden wir in sogenannte Stamm- und Produktionsstücklisten. Eine Stammstückliste dient dabei als eine Art Mustervorlage für die eigentliche Produktionsstückliste.
Sie enthält alle Stammdaten wie zugehörige Materialien, die Arbeitspläne mit den benötigten Zeiten für die Arbeitsschritte. Liege-, Warte- und mögliche Überlappungszeiten.
Da der Stücklistenkopf (ID-Schlüssel und Bezeichnung) durch die rekursive Funktion in der Materialwirtschaft abgelegt wird, kann er auch in andere Stücklisten wie ein Materialstammsatz wiederverwendet werden.
Durch diese Vorgehensweise ist es auch möglich, für Unterstücklisten separate Produktionsaufträge auszulösen oder sie extern fertigen zu lassen. Die Netzplantechnik würde eine Bestellbestand erkennen und die Stückliste nicht weiter auflösen.
Alle Positionen einer Stückliste sind nachträglich bis zur Erstellung der Fertigungspapiere dynamisch veränderbar. Auch hier erkennt die Netzplantechnik die Veränderungen.
Das apintra® Stücklistenwesen bietet einzigartig eine Reihe von Möglichkeiten für die Variantenverarbeitung:
Eine Stammstückliste wird für einen neuen Produktionsauftrag durch Duplizierung erzeugt. Die daraus entstandene Produktionsstückliste kann dann beliebig verändert werden.
Dieses geschieht durch einfaches Editieren der Produktionsstückliste (also löschen und/oder hinzfügen von Materialien, Arbeitsplänen und Zeiten)
Um eventuell eine Historie nachvollziehbar zu gestalten kann das auch durch Verwendung von Plus- / Minus-Stücklisten erfolgen.
Die Korrekte Auflösung der Material- und Zeitbedarfe übernimmt die Netzplantechnik.
[Eine Produktionsstückliste kann grundsätzlich auch aus einer anderen Produktionsstückliste erzeugt werden]
Im Stammstücklistenprozessor können in den Feldern Anzahl, Länge und Breite Buchstaben mit Formeln hinterlegt werden. Verwendet werden können beliebige Buchstaben die rekursiv abgearbeitet werden (von oben nach unten) und nachfolgende Mathermatik berücksichtigen:
- Addition +
- Subtraktion –
- Multiplikation *
- Division /
- Modulo %
- Potenz ^
- Größer >
- Kleiner <
- Aufrunden ~
Bei Erzeugung einer Produktionsstückliste wird die Stammstückliste rekursiv aufgelöst und die Formeln in Absolutwerte umgerechnet.
Der Produktionsprozessor: automatisch präzise
Der Produktionsprozessor ist die Steuerzentrale für das Produktswesen. Hier befindet sich rekursiv generierte Stückliste mit allen Materialen, Arbeitsplänen und Zeitbedarfen für die einzelnen Kapazitätsstellen.
Im Produktionsprozessor können die einzelnen Produktionsaufgaben freigegeben und die Arbeitspapiere erzeugt werden. Bis zu diesem Zeitpunkt sind Änderungen in Materialbereich und im Arbeitsplan ohne Probleme möglich.
Werden Änderungen im Produktionsprozessor und somit im Produktsablauf, der Materialzusammenstellung oder Größe vorgenommen, dann erkennt das die Netzplantechnik und verändert alle Abhängigkeiten – vom Materialbedarf (für das Bestell- und Lagerwesen) bis hin zu den Kapazitätsreservierungen für Personal und Maschinen.
Auch wenn für eine im Produktionsprozessor enthalten Unterstückliste eine Bestellung ausgelöst wird, weil die Baugruppe zugekauft werden soll, erkennt die Netzplantechnik dieses und erkennt, dass der Bedarf der Materialien für diese Baugruppe nicht mehr besteht. Der Bedarf wird dementsprechend reduziert.
Dabei arbeitet unsere Netzplantechnik nicht nach den sonst üblichen Verfahren des NetChange, denn die sind uns zu ungenau. Damit das System jederzeit korrekt und optimal auf Veränderungen reagiert, kalkulieren wir jeweils den kompletten neuen Netzplan (Material und Zeiten).
Durch Hinzuziehung von Wirkungsgraden sowohl beim Material als auch bei Kapazitäten wird das System für Neuberechungen optimiert und die Aussagekraft präziser.
Der Rechenprozess beginnt je nach Bedarf entweder bei den Startvorgängen und setzt von diesen ausgehend den frühestmöglichen Starttermin der nachfolgenden Vorgänge fest (Vorwärtsplanung) oder bei den letzten Vorgängen des Netzes (die keinen Nachfolger mehr haben) und setzt dann die spätesten Fertigstellungstermine der jeweils vorgelagerten Vorgänge fest (Rückwärtsplanung). Durch Kombination beider Methoden, ausgehend von einem definierten Start- und einem definierten Endtermin, ergeben sich dadurch für jeden Vorgang neben der Dauer folgende vier weitere wichtige Eigenschaften:
- Frühester Anfangszeitpunkt (FA) (aus Vorwärtsplanung)
- Frühester Endzeitpunkt (FE) (aus Vorwärtsplanung und jeweiliger Dauer)
- Spätester Endzeitpunkt (SE) (aus Rückwärtsplanung)
- Spätester Anfangszeitpunkt (SA) (aus Rückwärtsplanung und jeweiliger Dauer)
Pufferzeit: Die Pufferzeit ist ein zeitlicher Spielraum für die Ausführung eines Vorganges, so genannte Zeitreserven. Dieser Spielraum kann durch Verschiebung des Vorganges und/oder durch Verlängerung (Dehnung) der Vorgangsdauer genutzt werden.
Mit dem Modul BDE (Betriebsdatenerfassung), PZE (Personalzeiterfassung) und MDE (Maschinendatenerfassung) erhalten Sie Funktionen zur Erfassung von Betriebs- und Personalzeitdaten.
Die Erfassung der Zeiten erfolgt über elektronische Zusatzgeräte. Diese werden entsprechend den hinterlegten Arbeitszeitmodellen verarbeitet. Schnittstellen zur weiteren Verarbeitung in Lohn- und Gehaltsprogrammen stehen selbstverständlich zur Verfügung. Auch können unterschiedliche Arbeitszeitmodelle und Funktionen zur Gleitzeit und Akkordabrechnung definiert werden.
Zur Identifikation des jeweiligen Beschäftigten gibt es abhängig vom Erfassungsmedium unterschiedliche Varianten: RFID, Barcode und Magnetkarte. Eine Erweiterung hinsichtlich Zugangskontrolle ist optional möglich.
Das BDE Modul erfasst alle Betriebsdaten des Unternehmens. Zeiten, die einem Produktionsauftrag zuzuordnen sind, werden mit den verbrauchten Zeiten und den “tatsächlichen” Kosten den Verursachern zugeordnet. Störgründe, Unterbrechungen und Stückzahlen werden dabei erfasst. Auswertungen gibt es für Produktionsaufträge und Kapazitätsstellen. Der Wirkungsgrad einer Kapazitätsstelle wird automatisch optimiert und die Daten im Netzplan verarbeitet. Arbeitsfortschritt, Auftragsstatus und alle auftragsbezogenen Arbeitsleistungen sind jederzeit ersichtlich.
Zur Ergänzung ist eine vollautomatische MDE (Maschinendatenerfassung) optional einsetzbar. Auch lassen sich die BDE/MDE Module problemlos mit einem graphischen Leitstand koppeln.
Starten Sie Ihre Entwicklung noch heute: Sprechen Sie uns an!
